Capabilities
MicroPhase Coatings, Inc has extensive developing customized formulations for the unique needs of each customer. Our technology base includes siloxane, silane, and epoxy/silane hybrid coatings.
Our primary focus is surface modification of substrate surfaces. This includes hydrophobic, super hydrophobic, anti-icing, and corrosion protection.
The unique technologies we have developed allow for the products to be used in harsh environments where abrasion, chemical resistance, and thermal exposure are issues for traditional coatings.
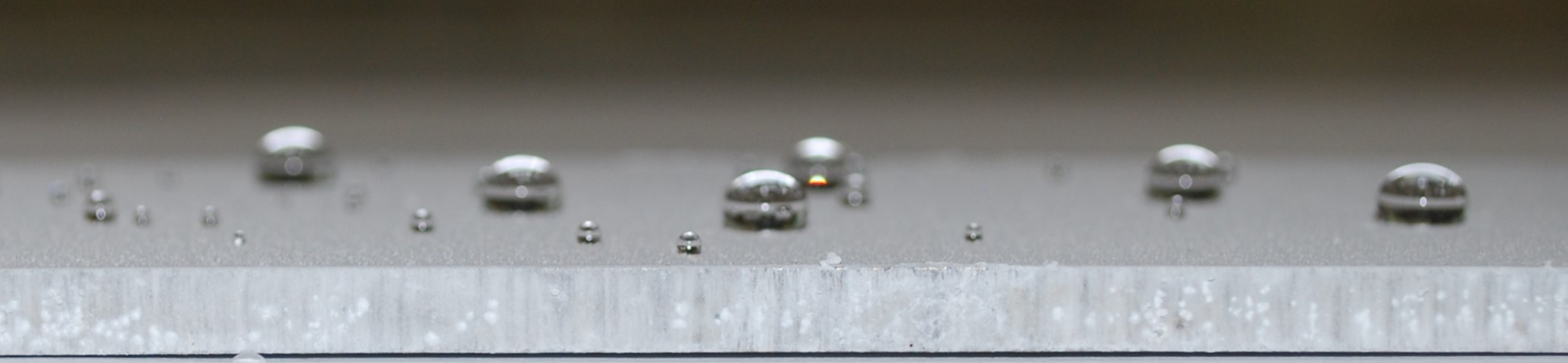
Customized Formulations
Superhydrophic coatings
A satellite dish manufacturer was using a super hydrophobic coating on their dishes, but was having extreme applications issues with the product. The customer approached MicroPhase Coatings about custom formulation. Working on contract with the customer we were able to develop a product that exceeded the specifications of their current product and eliminated the application issues they were experiencing. This product has been applied to millions of satellite dishes used around the world for data communications.
Hydrophobic coating for glass
MicroPhase Coatings was approached by a company selling hydrophobic coatings to the glass manufacturing industry. Working closely with the customer we developed a new technology for hydrophobic surface treatments on glass. The product has improved chemical and abrasion resistance and exceeds the contact angle and slide angle requirements of the previous product.
Anti-icing coating for aerospace
Working with the US Air Force, MicroPhase Coatings developed a technology to prevent the accumulation of ice on aircraft structures. The coating was adopted by an aircraft manufacturer and used to prevent ice accumulation around sensors located on the surface of the aircraft. The technology has also been adopted for use on ski lifts to prevent ice damage to the structures.
Thermal Barrier Coatings
Working on a project with the Joint Strike Fighter program, MicroPhase developed a thermal barrier coating to protect titanium and composite parts of the aircraft. This technology was then adopted by a jet engine manufacturer to protect components subjected to temperatures of 1700oF with corrosive environments.